A Comprehensive Overview to the Types of Ceramic Finish on the Market
Ceramic coverings have actually arised as a pivotal option throughout various industries due to their unique residential properties and applications. As we discover the unique qualities and applications of these finishings, the effects for efficiency and longevity end up being increasingly evident, raising questions about which type may best match your demands.
Comprehending Ceramic Coatings
Ceramic finishings are sophisticated safety remedies that have acquired popularity in different sectors, especially in automobile and aerospace applications. These coatings consist of a fluid polymer that, when treated, develops a resilient, hydrophobic layer externally of the substratum. This layer gives improved resistance to environmental impurities, UV radiation, and chemical exposure, thus prolonging the life and aesthetic appeal of the underlying material.
The basic part of ceramic coatings is silica, which adds to their hardness and resilience. The application procedure commonly includes surface prep work, application of the finish, and treating, which can be achieved via warmth or UV light. When healed, ceramic finishes exhibit phenomenal bonding homes, allowing them to stick strongly to a variety of surface areas, including steels, plastics, and glass.
Along with their protective features, ceramic finishings likewise provide simplicity of maintenance. Their hydrophobic nature reduces the adherence of dirt and gunk, making cleaning less complex and much less frequent. Generally, the fostering of ceramic layers stands for a substantial innovation in surface protection modern technology, supplying both practical and aesthetic advantages across several markets.
Kinds Of Ceramic Coatings
Different sorts of ceramic coatings are readily available, each made to meet particular performance demands and applications - Car Detailing. One of the most common kinds include:
Silica-based Coatings: These finishes primarily include silicon dioxide and are understood for their toughness and chemical resistance. They are commonly used in automobile and industrial applications.
Titanium Dioxide Coatings: Prominent for their photocatalytic homes, titanium dioxide finishings are frequently used in settings where self-cleaning and antifungal residential or commercial properties are preferable, such as in building products and vehicle surfaces.
Zirconia Coatings: Defined by their high-temperature stability and thermal resistance, zirconia coverings are utilized in applications such as generator engines and high-performance vehicle elements.
Alumina Coatings: Exhibiting excellent solidity and thermal security, alumina finishes are often made use of in wear-resistant applications, consisting of reducing devices and industrial machinery. - Auto Detailing
Crossbreed Coatings: Incorporating the buildings of different materials, hybrid layers use improved efficiency qualities, making them suitable for distinct and requiring applications.
Each sort of ceramic coating offers distinct objectives, enabling users to pick the most proper service based upon particular ecological conditions and efficiency needs.
Advantages of Ceramic Coatings
Ceramic finishes, in particular, deal various advantages that make them significantly preferred amongst makers and consumers alike. These coverings are immune to scratches, chemicals, and UV rays, making sure that the underlying surface area remains protected over time.
In addition to toughness, ceramic coatings offer exceptional hydrophobic residential or commercial properties, permitting very easy cleansing and upkeep. This water-repellent nature minimizes the adherence of dirt, grime, and other impurities, which can extend the visual allure and capability of imp source the surface. Furthermore, ceramic layers can dramatically boost thermal resistance, making them perfect for applications that endure high temperatures.
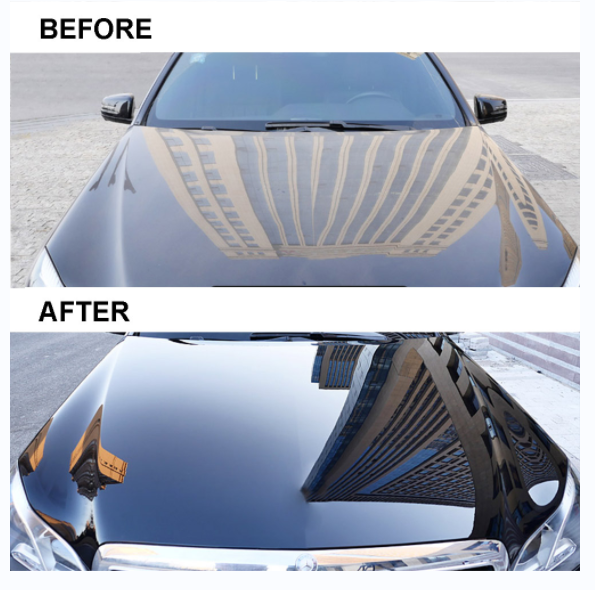
Application Refine
When using ceramic finishes, a precise method is important to attain ideal outcomes. A clean surface area makes certain correct attachment of the coating.
Once the surface area is prepped, the next step is to apply the ceramic finishing. This can be done making use of an applicator pad or a microfiber towel, guaranteeing even coverage. It is crucial to function in small areas to preserve control and prevent early treating. The coating needs to be applied in slim layers, as thicker applications can result in irregular coatings.
After application, the finish requires a specific curing time, generally varying from a few hours to a complete day, depending on the item. Complying with these actions faithfully will maximize the effectiveness and long life of the ceramic coating, offering a resilient protective layer for the surface.
Maintenance and Longevity
To make sure the durability and performance of a ceramic coating, normal maintenance is essential. Ceramic finishes, known for their durability and protective top qualities, call for particular treatment regimens to optimize their lifespan and performance.
Along with routine washing, regular inspections are important. Seek indicators of wear or damage, such as hydrophobic buildings decreasing or surface blemishes. If essential, a light gloss may be related to renew the covering without stripping it away.
In addition, the application of a booster spray can enhance the layer's hydrophobic effects and recover its gloss. This is especially helpful for layers that have actually remained in usage for an extensive duration. Inevitably, by sticking to these review upkeep methods, one can dramatically expand the life of a ceramic layer, ensuring that it remains to offer optimal protection against environmental aspects and maintain the aesthetic charm of the vehicle.
Conclusion
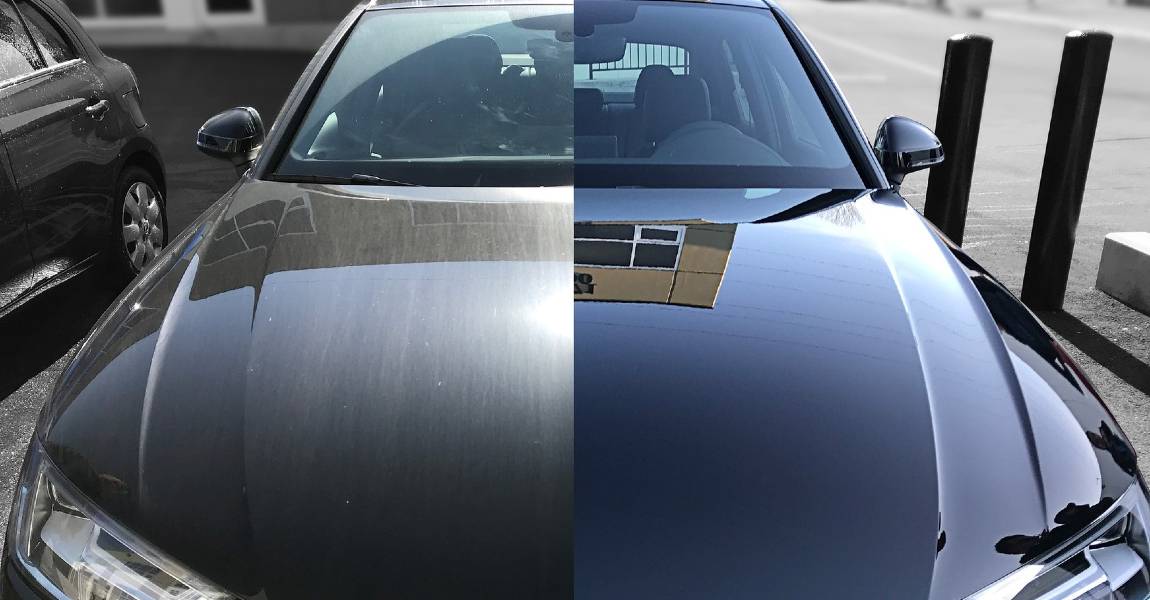